مراحل طراحی و ساخت قالب دایکاست
قالب دایکاست که به آن ریخته گری تحت فشار هم گفته می شود، یکی از پرکاربردترین روش ها در ساخت و تولید قطعات فلزی در صنایع گوناگون می باشد. برخلاف روش قالب تزریق پلاستیک که برای تولید قطعات پلاستیکی از آن استفاده میشود اما قالب دایکاست برای تولید قطعات فلزی کاربرد دارد. در روش ساخت قالب دایکاست در تهران، قطعات فلزی را مطابق با اصول کلی ریخته گری تولید می کنند و در ابتدا پس از ذوب کامل مواد، آن را به درون قالب تزریق کرده و مواد از حالت مایع به جامد منجمد می شوند.
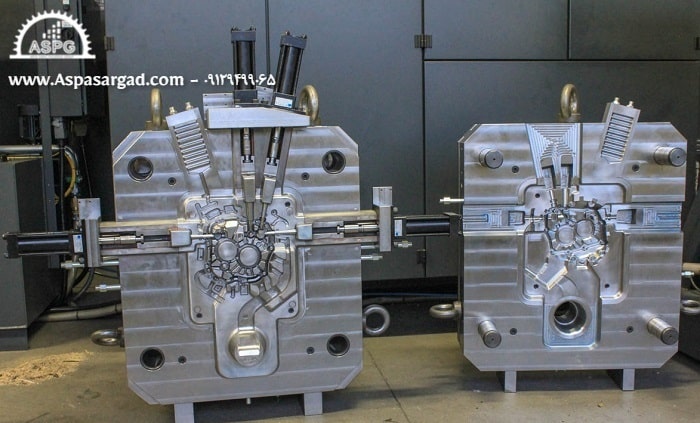
امروزه طیف بسیار متنوعی از قطعات المینیومی به روش دایکاست ساخته میشود که به کاهش وزن قطعات تولیدی کمک میکند. پیچیدگی چنین قطعاتی باعث میشود که ساخت قالب دایکاست به تیمی متبحر و با تجربه سپرده شود که معمولا هزینه ساخت ان نیز بالا میباشد . در این روش باید تنشهای مکانیکی و حرارتی بالا که در قطعات قالب ایجاد میشود محاسبه شود و از فولادی استفاده شود که در برابر تمام این تنش ها مقاوم بوده تا حد مقدور از ترکخوردگی زودهنگام قطعات قالب جلوگیری شود.
قالب دایکاست چیست؟
ساخت قالب دایکاست یا دیکست مولد یک فرایند تولید قالبهای فشرده است که به وسیله آن قطعات دقیق و با کیفیت بالا تولید میشوند. این فرایند در صنعت تولید اتومبیل، اسباب بازیها و محصولات دیگر استفاده میشود .در این صنعت، یک قالب فشرده برای تزریق مواد مختلف استفاده میشود. قالب فشرده معمولاً از فلزات مانند فولاد سخت تهیه میشود و دارای یک تراشه با دقت بالا است. این تراشه دارای فرم قطعه مورد نظر است و هنگامی که مواد فشرده درون قالب تزریق میشوند، قطعه نهایی به شکل مورد انتظار تولید میشود.
فرایند تولید قالب سازی دایکاست
فرایند تولید دیکست مولد شامل چند مرحله است. در ابتدا، یک طرح طراحی میشود که شامل ابعاد دقیق و جزئیات قطعه نهایی است. سپس، قالب فشرده بر اساس این طرح تهیه میشود. این قالب میتواند از چندین قسمت تشکیل شده باشد که به وسیله تراشکاری، فرزکاری و دیگر روشهای تراشهسازی ساخته میشود. در نهایت، قالب فشرده برای تزریق مواد فشرده استفاده میشود و قطعه نهایی با دقت بالا تولید میشود.
مراحل ساخت قالب
مراحل ساخت قالب diecast شامل استفاده از کوره ، فلز، ماشین ریختهگری و die است. فلزی (آلومینیوم یا روی) در کوره ذوب شده و سپس با فشار بالا به محفظه در دستگاه ریخته گری تزریق میشود. فشار تزریق بسته به وزن قطعه و نوع ماده ذوب شد تزریقی، بستگی دارد.
دو نوع اصلی از ماشینآلات ساخت قالب دایکاست وجود دارد: ماشینآلات اتاق گرم (برای آلیاژهای با دمای پایین ذوب، مانند روی) و ماشینآلات اتاق سرد (برای آلیاژهای با دمای بالا ذوب، مانند آلومینیوم). تفاوت بین این ماشین ها در بخشهای مربوط به تجهیزات و ابزار دقیق خواهد بود. با این حال، در هر دو ماشین، پس از اینکه فلزمذاب به قالب تزریق میشود، آن را به سرعت خنک میکند و به قسمت نهایی، یعنی diecast، تبدیل میکند. مراحل این فرایند در بخش بعدی شرح داده شده است.
ماشین آلات اتاق گرم در حالت باز و بسته
diecast که در این فرایند تولید میشوند به شدت در اندازه و وزن متفاوتاند (از چند اونس تا 100 پوند). یک کاربرد معمول از قطعات این صنعت ضمایم housings – thin-walled (محوطههای دیوار نازک) است، که اغلب نیاز به ribs و bosses در محوطه دورنی دارد. دیگر قطعات دایکاست propellers, gears, bushings, pumps, و valves است. چند اجزای خودرو که با استفاده از diecast ساخته میشوند: پیستون، سر سیلندر و بلوکهای موتور.
هزینه ساخت قالب دایکاست
جهت بالا بردن کارایی و افزایش طول عمر قالب دایکاست، باید از فولاد با کیفیت و مقاوم در برابر حرارت که به اصطلاح به ان فولاد گرم کار گفته میشود استفاده کرد که با ضخامت زیاد و مشخصات فنی دقیق باید قالب دایکاست را از ان ساخت. این نوع قالب از دو نیمه ثابت و متحرک ساخته میشود. دو نیمه قالب در یک ماشین ریختهگری باید در دماها و فشارهای مورد نیاز کار کنند بسته میشود تا قطعهای با کیفیت و مطابق با مشخصات کارفرما تولید شود.
هزینه ساخت قالب دایکاستدر قالب سازی به ویژگیها مانند اندازه ، تعداد حفرهها، تعداد هسته یا اسلایدهای مورد نیاز، وزن قالب، نوع هندسی و پیچیدگی قطعه، پرداخت و آبکاری و البته تصمیمات نهایی برای ساخت قالب دایکاست که باید بین مشتری و قالب ساز مورد بحث و بررسی قرار گیرد بستگی دارد.
انواع قالبهای ریختهگری متنوعی که هر کدام یکی از نیازهای مشتری را برآورده میکند وجود دارد. انتخاب نوع قالب دایکاست بسته به نیاز کارفرما میتواند یکی از این موارد باشد:
1- اندازه قطعه برای ریختهگری 2- حجم قطعات مورد نیاز 3-کیفیت مورد نظر 4- قطعات مجموعهای
خطوط جداسازی قطعات و محصولات دایکاست
یکی از مهمترین پارامترهای طراحی قالبهای دایکاست تصمیمگیری در مورد نوعی از خط جدایی است که قطعه را شکافته و سطح تماس بین دو یا چند جزء را ایجاد میکند. جایی که طراح این خط را قرار میدهد به اشکال هندسی و میزان تحمل سطوح مختلف بستگی دارد. طراح دو انتخاب دارد یا یک خط جدایی مستقیم یا یک خط جدایی شکسته. باید سعی کنید قطعات را با خط جداکننده مستقیم طراحی کنید زیرا از نظر هزینه ابزار، کم هزینهترین گزینه است. هنگام تصمیمگیری در مورد خط جدایی، طراح باید عوامل زیر را در نظر بگیرد:
سفارش مشتری – معمولاً مشخصات قطعه یا محصول مشتری، قرار دادن خط جداسازی را به چالش میکشد. الزامات اجباری مشتری نیز به یک مسأله تبدیل میشود
برآورد هزینههای قالب – یک خط جداکننده مستقیم میتواند هزینه ابزارآلات را کاهش دهد. با این حال، در برخی موارد، طراحی یک خط جداکننده شکسته مقرون به صرفهتر خواهد بود زیرا در غیر این صورت ویژگیهایی که در قطعه مورد نظر وجود دارد شما را مجبور به راهاندازی خط جدیدی میکند که باعث یک هزینه سربار میباشد.
ماشینکاری و پرداخت – بیشتر قطعات نیاز به ماشینکاری پس از تولید دارند. قسمتهای از قطعه نیاز به کارهای تکمیلی و ماشین کاری دارند . ضمناً این قسمت نباید نیاز به زیبایی داشته باشد زیرا اثرات پرداختهای نهایی بر روی قطعه نمایان میشود.
جریان فلز مذاب – کیفیت تزریق فلز مذاب به محل مناسب ورودی قلب بستگی دارد. ورودی قالب باید روی خط جداکننده طراحی شود. این کار سه حسن دارد اول اینکه تعیین میکند که آیا قالب ریختهگری به درستی با فلز مذاب پر میشود. دوم تحت ریختهگری فشار بالا، مکانیزم تزریق یا پر کردن میتواند فلز را به درون ریختهگری فشار دهد تا از جمع شدن قطعه در طول انجماد جلوگیری کند و سوم اینکه با پرداخت خط جداکننده ورودی قالب نیز پرداخت شود
هستهها – موقعیت هستهها (هستهها سوراخهایی را در قطعه ایجاد میکنند) محل قرارگیری خط جداسازی را تعیین میکنند. طراح باید محل هسته و همچنین اندازه قطر و طول هر هسته را برای هر سوراخ مورد نیاز در ریختهگری در نظر بگیرد.
طی فرایند طراحی قالب دایکاست جریان مذاب از مهمترین ملاحظات میباشد. اگر قالب به دقت پر نشود منجر به نقصهایی در قطعه خروجی میشود این نقصها به شکل خطوط سطحی و یا حفرههای هوا به صورت مک داخلی بر روی قطعه نمایان میشود که باعث کاهش استحکام و زیبایی قطعه میشود.
همچنین طراح باید پران ها را که قطعه را از قالب خارج میکند در طراحی خود مورد توجه قرار دهد. پران ها باید طوری طراحی شوند که حداقل علائم را بر روی قطعه برجا بگذارند. یکی از حسنهای پران جلوگیری از خم شدن قطعه میباشد. اثرات پین پران بر روی قطعات به صورت فشرده یا برجسته در حدود 0.3 میلیمتر میباشد. قطر نشانههای پین پران بسته به اندازه ریختهگری متفاوت خواهد بود.